“Smart consumer devices remain accessible to tech-savvy Gen Z or young millennial homeowners who can purchase components from Amazon and configure DIY smart home solutions. However, I ...
Decentralized Manufacturing Platform Makes Housing Production More Accessible for Builders


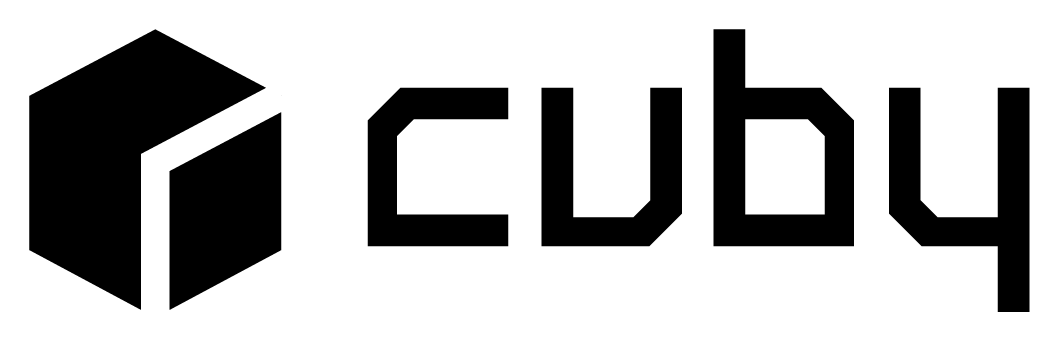
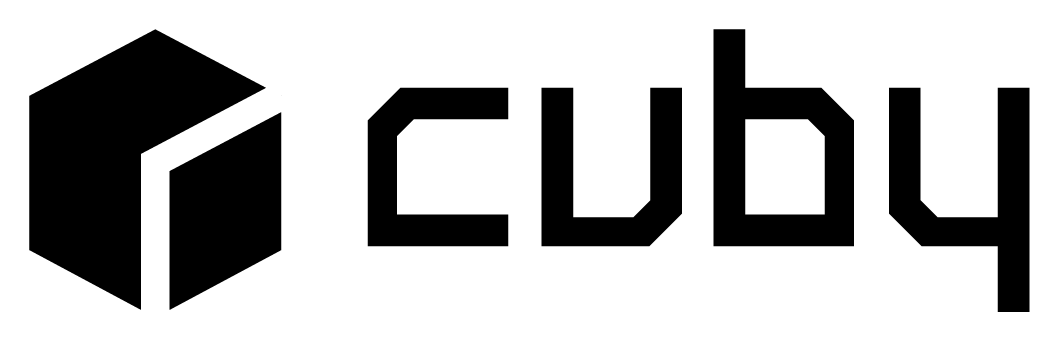
In an era where housing affordability has become a critical bipartisan issue, one company is taking an innovative approach to solving America’s construction crisis. Cuby, co-founded by CEO Aleh Kandrashou and COO Aleksandr Gampel, is challenging traditional construction methods with their innovative mobile manufacturing concept – a system that crucially offers lower costs than traditional construction methods from day one.
Gampel, who runs the business side of Cuby while Kandrashou leads the technical vision, brings both real estate heritage and engineering expertise to the venture. His journey to co-founding Cuby began with a frustration familiar to many developers – the inability to find suitable solutions for building more efficiently. This challenge would eventually lead him to reimagine the entire construction process, but first, he had to understand the depth of the industry’s labor crisis.
The urgency of their mission becomes clear when considering the current state of construction labor. While many overlook the highly skilled nature of the profession, Gampel emphasizes this crucial point: “There’s stigma around someone being a construction worker, but most people don’t realize it’s such a highly skilled profession.”
But with worker efficiency down 40% since 1970, and an estimated 41% of the workforce retiring by 2031, the industry faces a critical challenge. Only one new worker enters the field for every seven leaving, partly due to changing career preferences.
This workforce challenge shaped Cuby’s distinctive approach. While major players like Graystar are investing in volumetric modular facilities and others focus on traditional prefab solutions requiring massive centralized factories, Cuby has developed a distributed network of production facilities that can be deployed within 200 miles of construction sites, dramatically reducing logistics costs while maintaining efficiency.
Each facility operates as a standalone business, typically in partnership with established local operators – whether homebuilders, general contractors, or family offices with manufacturing experience. These partners often serve as primary customers for the factory’s output, though third-party builders can also purchase homes. The operations are streamlined for maximum impact: each site can produce approximately 200 single-family homes annually, employing 265-275 workers who handle everything from foundation to interior finish, effectively replacing the traditional network of 22 subcontractors typically required for home construction.
Cuby’s manufacturing process represents a significant breakthrough in construction efficiency. “We’ve developed a hardware and software-enabled process that breaks down construction steps, similar to Toyota’s production system,” Gampel explains. “This allows us to use unskilled labor while actually reducing the total labor hours required to build a home.” The process begins with component manufacturing at their facilities, followed by systematic assembly at the construction site using Cuby’s trained workforce.
Beyond efficiency, Cuby’s approach tackles another critical industry barrier: regulatory compliance. “In the US, there’s 26,000 different zoning codes,” Gampel notes. “Instead of designing something that requires regulatory changes, we’ve designed our system to be code compliant from day one while still delivering the same exact home that any production home builder builds on site.” This strategic decision has proven crucial for adoption by traditional industry players and their lenders, who tend to be conservative when it comes to construction innovation.
The push toward industrialized construction isn’t entirely new – from Sears catalog homes to Levittown developments, the industry has long sought more efficient building methods. But today’s market forces are creating unprecedented pressure for innovation. As Gampel sees it, rising costs and labor constraints are forcing the industry to adapt. “The world’s getting to a point where costs are going up,” he notes, citing potential implications of new administration policies, further labor losses, and possible tariffs on imported materials. While major players like Graystar are investing in their own modular facilities, they represent a unique case with thousands of units in their pipeline. For most builders, the challenge has been finding solutions that don’t require massive balance sheet investments – a gap Cuby’s distributed manufacturing model aims to fill.
Building on this foundation, Cuby’s approach to scaling is equally methodical. The company worked backwards from their ambitious goal of deploying 275 production facilities over the next decade, carefully designing a business model that accounts for incumbent incentives and cost of capital considerations. They already have their first scaled-down version operational and a major contract in Nevada that they can publically speak about. “We feel like we’ve taken 90% of the technical risk off the table,” Gampel states. “Going forward, it’s all about execution and operational risk.”
“It’s hard to be a first world country when 50% of the US population can’t afford a $250,000 home,” Gampel observes. Through their growing network of distributed manufacturing facilities, Cuby is working to make affordable housing a reality for millions of Americans – transforming not just how homes are built, but who can afford to own them.
Similar Articles
Explore similar articles from Our Team of Experts.
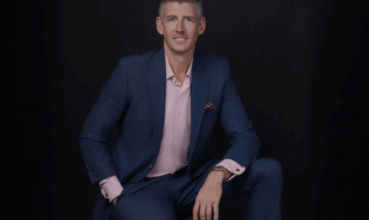
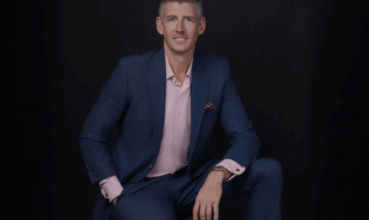
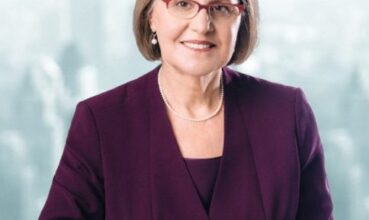
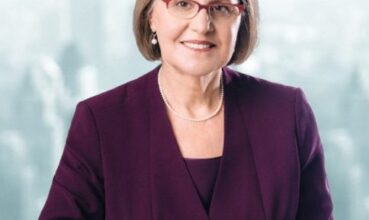
Thirty years after authoring groundbreaking books on lending discrimination under President Clinton’s White House executive order, mortgage industry expert Anna DeSimone has witnessed ...
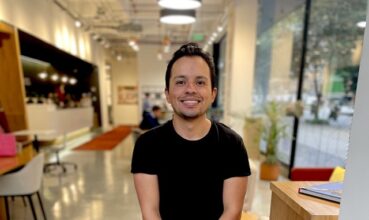
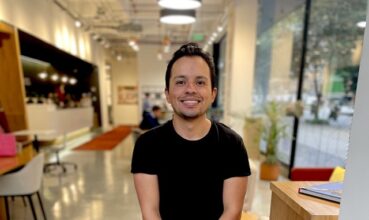
“Why are we doing this the same way we have for the last 100 years?” This question haunted Andrés Leal during his early days as a civil engineer, watching crews lay bricks and r...
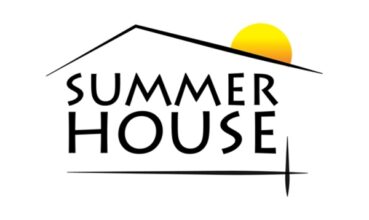
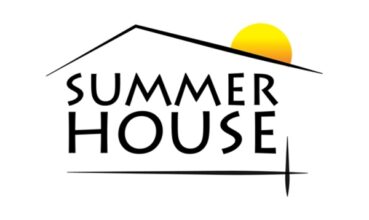
In an era when environmental consciousness often feels like a marketing exercise, Rodney Mendez and Summer House are proving that authentic ecological development can command a premium in th...
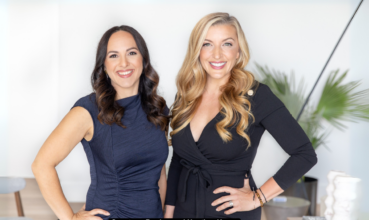
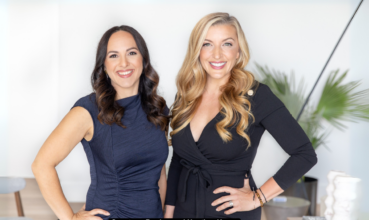
ACME Real Estate founder Courtney Poulos has earned a reputation as one of real estate’s most dynamic innovators. A two-time HousingWire Woman of Influence (2020, 2023), Forbes Real Es...