When Mana Mohammadkhani left Tehran 16 years ago to pursue graduate studies at USC, she couldn’t have predicted the journey that would lead her to establish one of Brooklyn’s inn...
Modular Housing Pioneer Aims to Make Home Ownership Attainable


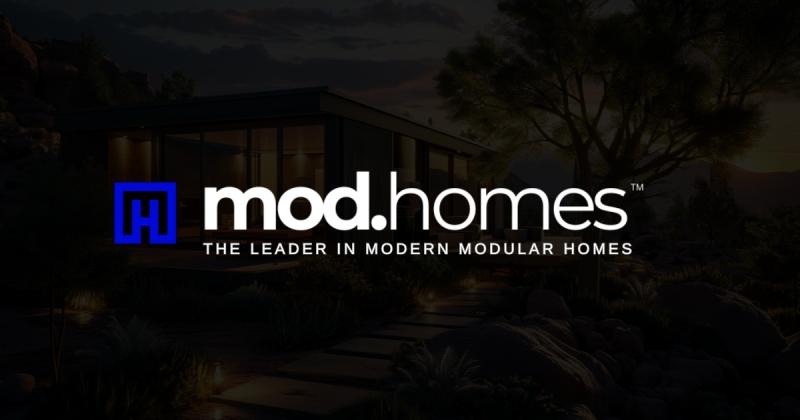
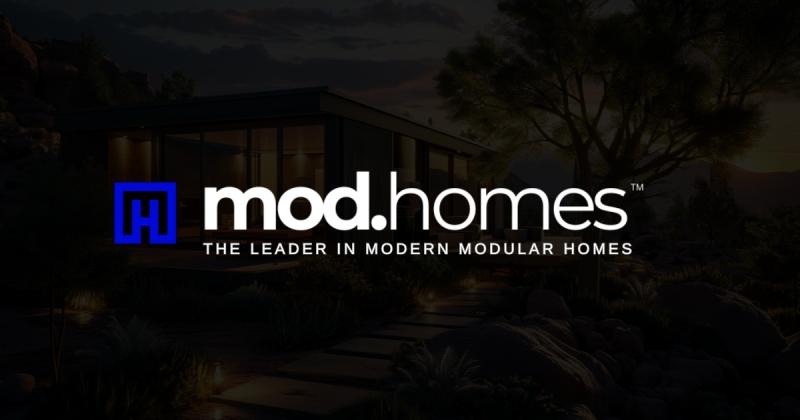
In an era where housing affordability has reached crisis levels, Bryan Farris is tackling the challenge through innovation in modular construction. As CEO and Co-Founder of Mod.Homes, Farris is pioneering what he calls “housing as a service” – a new approach to providing quality, attainable housing solutions that could reshape how we think about home ownership.
The venture, launched about a year ago after three and a half years of market research, emerged from a deeply personal concern: where would his children be able to afford to live? Farris, a father of six ranging from 23 to 12 years old, and his business partner, who also has multiple children including 23-year-old twins, watched as their home state of Utah – traditionally an affordable market – became increasingly expensive.
“We can’t just scroll them out further and further and push them out of our own backyards,” Farris explains. Initially, they thought the problem was merely a disconnect between supply and demand, but deeper research revealed a more fundamental issue: the market lacked products that could effectively serve the attainable housing segment.
Mod.Homes’ distinctive approach centers on flexible living spaces that can expand on-site. Rather than traditional container homes, which Farris notes are “really short, really narrow,” Mod.Homes creates what they call “FlexLux” homes – semi-permanent structures designed for various uses from disaster recovery to workforce housing. Notably, these aren’t homes on wheels; they’re designed to provide stable, quality housing while maintaining flexibility in deployment.
The company sets itself apart through technological innovation. Their “Ready Prevent” platform, developed in partnership with Google Ventures, helps potential buyers navigate the complex world of zoning requirements and create feasibility studies. The system integrates various APIs to generate site plans showing setbacks and zoning requirements – addressing one of the biggest obstacles in modular home deployment.
Manufacturing takes place internationally, with facilities in Mexico and China, though design work remains U.S.-based. To ensure quality control, Mod.Homes partners with Bridge Pipeline Sourcing Group, maintaining boots on the ground at manufacturing facilities. This approach allows them to maintain high standards while keeping costs manageable.
One of their most innovative initiatives is the “Prosper Village” model, which aims to transform struggling mobile home parks rather than replace them. “Every kid deserves a place that they can be proud to say they came from,” Farris asserts. The company specifically introduces new amenities and quality homes without displacing existing residents or raising fees to unjust levels. “We can still use that underutilized property and just make it better. Make it kind of a rising-tide-lifts-all-boats,” Farris explains.
Sustainability is built into their approach. The homes incorporate cutting-edge off-grid technologies, including hydropanels that extract water from air humidity (developed at Arizona State University) and advanced solar power systems. These features not only promote environmental responsibility but also make quality housing possible in areas with limited infrastructure.
While Farris acknowledges they don’t have “the only answer” to the housing crisis, Mod.Homes’ approach shows promise in making quality housing more attainable. Their target market isn’t the luxury short-term rental sector but rather working families struggling to find affordable housing – like the single mother working two jobs as a Walmart cashier. As he puts it, they’re following the starfish story philosophy – making a difference for as many people as they can, one home at a time.
Similar Articles
Explore similar articles from Our Team of Experts.
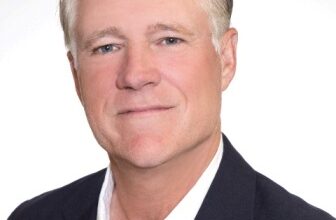
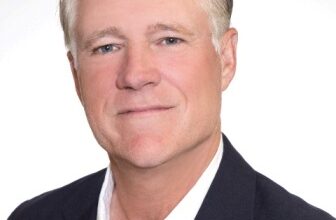
When Scott Spelker left his career in Wall Street foreign exchange in 2012, he was seeking more than just a career change. Following his instincts toward education, he invested two years in ...
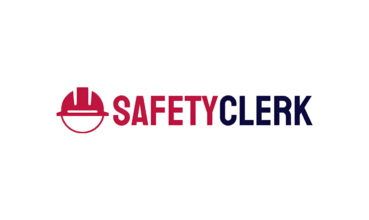
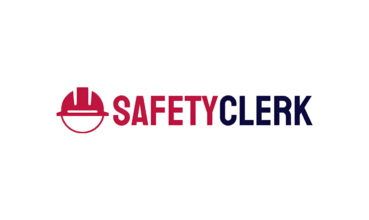
When a fraudulent workplace injury claim hit one of Stefano Braganti’s construction sites, the resulting years-long legal battle exposed a critical gap in the industry. As a structural...
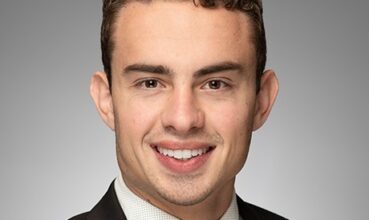
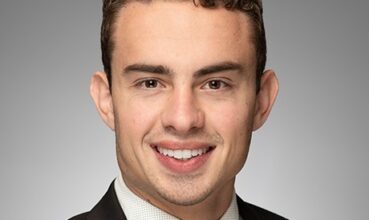
The multi-family real estate market in the Midwest is showing encouraging signs of recovery after a challenging 2023, according to Jack Friskney, a prominent multi-family broker at Marcus &a...
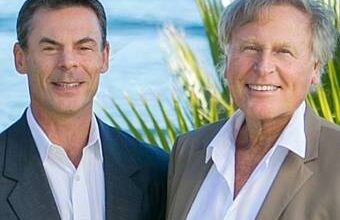
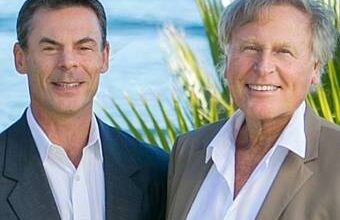
In the ever-changing landscape of Southern California’s luxury real estate market, Ty Bergman stands as a beacon of experience and adaptability. With roots tracing back to 1989, Bergma...